Сущность метода заключается во внедрении в поверхность образца (или изделия) алмазного конусного (шкалы А, С, D) или стального сферического наконечника (шкалы В, Е, F, G, H, К) под действием последовательно прилагаемых усилий предварительного и основного усилий и в определении глубины внедрения наконечника после снятия основного усилия ().
Обозначения параметров, их определения и схемы приложения нагрузки при определении твердости приведены в приложении 1.
(Измененная редакция, Изм. N 3). 1. ОТБОР ОБРАЗЦОВ 1.1. Толщина образца (или изделия) должна не менее чем в 10 раз превышать глубину внедрения наконечника после снятия основного усилия ().
Минимальная толщина образца или изделия определяется в соответствии с приложением 2. 1.2. Шероховатость поверхности образца (или участки для измерения твердости изделия) должна быть не более 2,5 мкм по ГОСТ 2789, если нет других указаний в нормативно-технической документации на металлопродукцию. 1.3. Образец должен быть подготовлен таким образом, чтобы не изменялись его свойства в результате механической или другой обработки, например, от нагрева или наклепа.
HRC шкала твердости по Роквеллу
Разд.1. (Измененная редакция, Изм. N 3).
Разд.2. (Исключен, Изм. N 3). 3. АППАРАТУРА 3.1. Приборы для измерения твердости должны соответствовать требованиям ГОСТ 23677.
Приборы для измерения твердости должны обеспечивать приложение усилий, приведенных в табл.1. Таблица 1
Шкала твердости | Обозначение единицы измерения | Предварительное усилие | Основное усилие | Общее усилие | Диапазон измерений, ед. твердости |
Н (кгс) | |||||
А | HRA | 98,07(10) | 490,3(50) | 588,4(60) | 20-88 |
В | HRB | 98,07(10) | 882,6(90) | 980,7(100) | 20-100 |
С | НRС | 98,07(10) | 1373(140) | 1471(150) | 20-70 |
D | HRD | 98,07(10) | 882,6(90) | 980,7(100) | 40-77 |
Е | HRE | 98,07(10) | 882,6(90) | 980,7(100) | 70-100 |
F | HRF | 98,07(10) | 490,3(50) | 588,4(60) | 60-100 |
G | HRG | 98,07(10) | 1373(140) | 1471(150) | 30-94 |
Н | HRH | 98,07(10) | 490,3(50) | 588,4(60) | 80-100 |
К | HRK | 98,07(10) | 1373(140) | 1471(150) | 40-100 |
3.2. Наконечник алмазный конусный типа НК по ГОСТ 9377, угол при вершине — 120°, радиус сферической части 0,2 мм.
3.3. Наконечник шариковый стальной. Номинальные диаметры шариков должны быть 1,588 (шкалы В, F, G) и 3,175 мм (шкалы Е, Н, К) по ГОСТ 3722. Шероховатость поверхности шарика — не более 0,040 мкм по ГОСТ 2789.
Предельные отклонения диаметров шарика не должны превышать:
±0,003 мм — для шарика диаметром 1,588 мм;
±0,004 мм — для шарика диаметром 3,175 мм.
3.4. Столик или подставка должны иметь твердость на опорных поверхностях не менее 50 HRC.
(Поправка. ИУС N 8-2002).
4. ИЗМЕРЕНИЕ ТВЕРДОСТИ 4.1. Измерение твердости проводят при температуре (20) °C. При разногласиях в результатах измерение твердости проводят при температуре (23±5) °С.
4.2. Опорные поверхности столика и подставки, а также опорные и рабочие поверхности образца (или изделия) должны быть очищены от посторонних веществ (окалины, смазки и др.).
4.3. Образец должен быть установлен на столике или подставке устойчиво во избежание его смещения и прогиба во время измерения твердости.
4.4. При измерении твердости прибор должен быть защищен от вибрации и ударов.
4.5. При измерении твердости должны соблюдаться условия:
плавное приведение наконечника в контакт с рабочей поверхностью образца (или изделия);
плавное приложение предварительного и основного (в течение 2-8 с) усилий; плавное снятие основного усилия через 1-3 с после резкого замедления или остановки стрелки индикатора (или изменения показаний цифрового отсчетного устройства).
Для металлов, при измерении твердости которых резкого замедления или остановки стрелки индикатора (или изменения показаний цифрового отсчетного устройства) не наблюдается, время выдержки под общим усилием должно составлять от 10 до 15 с.
При наличии указаний в нормативно-технической документации на металлопродукцию указанное время выдержки может быть увеличено до 60 с.
4.6. Расстояние между центрами двух соседних отпечатков должно быть не менее четырех диаметров отпечатка (но не менее 2 мм).
Расстояние от центра отпечатка до края образца должно быть не менее 2,5 диаметра отпечатка (но не менее 1 мм).
4.7. На опорной поверхности образца (или изделия) не должно наблюдаться следов деформации от отпечатка.
4.8. Число твердости по Роквеллу определяется по шкале индикатора или показателя цифрового отсчетного устройства с округлением до 0,5 единицы твердости.
4.9. При измерении твердости на выпуклых цилиндрических и сферических поверхностях по шкалам А, В, С, D, F, G в результаты измерения твердости должны быть введены поправки, величины которых приведены в приложении 3. Поправки прибавляются к полученным значениям твердости.
Поправки при измерении твердости на вогнутых поверхностях устанавливаются в нормативно-технической документации на металлопродукцию.
4.10. После смены наконечника, рабочего столика или подставки первые три измерения не учитываются.
4.11. Количество отпечатков при измерении твердости, способ обработки и результаты измерений указываются в нормативно-технической документации на металлопродукцию.
5. ПРОТОКОЛ ИСПЫТАНИЯ 5.1. В протоколе измерения твердости следует указать:
значения и шкалу твердости;
продолжительность выдержки индикатора под общей нагрузкой в случае отличия от стандартных условий;
Разделы 3-5. (Измененная редакция, Изм. N 3).
ПРИЛОЖЕНИЕ 1 (обязательное). ОБОЗНАЧЕНИЯ ПАРАМЕТРОВ, ИХ ОПРЕДЕЛЕНИЯ И СХЕМЫ ПРИЛОЖЕНИЯ НАГРУЗКИ ПРИ ОПРЕДЕЛЕНИИ ТВЕРДОСТИ ПРИЛОЖЕНИЕ 1
Обязательное
Таблица 2
Обозначение | Определение параметров |
Угол при вершине алмазного конусного наконечника, градус | |
Радиус сферической части алмазного конусного наконечника, мм | |
Диаметр шарика, мм | |
Предварительное усилие, Н (кгс) | |
Основное усилие, Н (кгс) | |
Общее усилие F0+F1 , Н (кгс) | |
Глубина внедрения наконечника под действием предварительного усилия, мм | |
Глубина внедрения наконечника под действием основного усилия, мм | |
Глубина внедрения наконечника после снятия основного усилия в единицах измерения 0,002 мм | |
HRA, HRC*, HRD | Твердость по Роквеллу по шкалам А, С и D — (100-е) единиц твердости |
HRB, HRE, HRF, HRG, HRH, HRK | Твердость по Роквеллу по шкалам В, Е, F, G, Н, К — (130-е) единиц твердости |
______________
* Твердость, измеренная по шкале С в соответствии с ГОСТ 8.064.
(Поправка. ИУС N 8-2002). Твердость по Роквеллу обозначают символом HR с указанием шкалы твердости, которому предшествует числовое значение твердости из трех значащих цифр. Например: 61,5 HRC — твердость по Роквеллу 61,5 единиц по шкале С.
(Поправка. ИУС N 8-2002). Черт. 1. Схема проведения измерения твердости при применении алмазного наконечника Схема проведения измерения твердости
при применении алмазного наконечника
Черт.1 Черт. 2. Схема проведения измерения твердости при применении стального наконечника Схема проведения измерения твердости
при применении стального наконечника
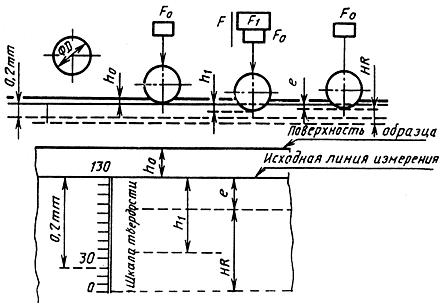
Черт.2 ПРИЛОЖЕНИЕ 2 (рекомендуемое) ПРИЛОЖЕНИЕ 2
Рекомендуемое Черт.3. Минимальная толщина образца в зависимости от шкалы и ожидаемой твердости при измерении твердости по шкалам А, С, D Минимальная толщина образца в зависимости от шкалы и ожидаемой
твердости при измерении твердости по шкалам А, С, D
Черт.3 Черт. 4. Минимальная толщина образца в зависимости от шкалы и ожидаемой твердости при измерении по шкалам B, E, F, G, H, K Минимальная толщина образца в зависимости от шкалы
и ожидаемой твердости при измерении по шкалам B, E, F, G, H, K
Черт.4
ПРИЛОЖЕНИЯ 1, 2. (Измененная редакция, Изм. N 3).
ПРИЛОЖЕНИЕ 3 (обязательное) ПРИЛОЖЕНИЕ 3
Обязательное Поправки, добавляемые к величинам твердости по Роквеллу,
при измерениях на выпуклых цилиндрических поверхностях 1. При измерениях по шкалам А, С, D
Таблица 3
Твердость по Роквеллу | Радиус кривизны , мм | ||||||||
3 | 5 | 6,5 | 8 | 9,5 | 11 | 12,5 | 16 | 19 | |
20 | 2,5 | 2,0 | 1,5 | 1,5 | 1,0 | 1,0 | |||
25 | 3,0 | 2,5 | 2,0 | 1,5 | 1,0 | 1,0 | 1,0 | ||
30 | 2,5 | 2,0 | 1,5 | 1,5 | 1,0 | 1,0 | 0,5 | ||
35 | 3,0 | 2,0 | 1,5 | 1,5 | 1,0 | 1,0 | 0,5 | 0,5 | |
40 | 2,5 | 2,0 | 1,5 | 1,0 | 1,0 | 1,0 | 0,5 | 0,5 | |
45 | 3,0 | 2,0 | 1,5 | 1,0 | 1,0 | 1,0 | 0,5 | 0,5 | 0,5 |
50 | 2,5 | 2,0 | 1,5 | 1,0 | 1,0 | 0,5 | 0,5 | 0,5 | 0,5 |
55 | 2,0 | 1,5 | 1,0 | 1,0 | 0,5 | 0,5 | 0,5 | 0,5 | 0 |
60 | 1,5 | 1,0 | 1,0 | 0,5 | 0,5 | 0,5 | 0,5 | 0 | 0 |
65 | 1,5 | 1,0 | 1,0 | 0,5 | 0,5 | 0,5 | 0,5 | 0 | 0 |
70 | 1,0 | 1,0 | 0,5 | 0,5 | 0,5 | 0,5 | 0,5 | 0 | 0 |
75 | 1,0 | 0,5 | 0,5 | 0,5 | 0,5 | 0,5 | 0 | 0 | 0 |
80 | 0,5 | 0,5 | 0,5 | 0,5 | 0,5 | 0 | 0 | 0 | 0 |
85 | 0,5 | 0,5 | 0,5 | 0 | 0 | 0 | 0 | 0 | 0 |
90 | 0,5 | 0 | 0 | 0 | 0 | 0 | 0 | 0 | 0 |
Примечание. Поправки более 3 единиц твердости по шкалам А, С, D не допускаются.
2. При измерениях по шкалам В, F, G Таблица 4
Твердость по Роквеллу | Радиус кривизны , мм | ||||||
3 | 5 | 6,5 | 8 | 9,5 | 11 | 12,5 | |
20 | 4,5 | 4,0 | 3,5 | 3,0 | |||
30 | 5,0 | 4,5 | 3,5 | 3,0 | 2,5 | ||
40 | 4,5 | 4,0 | 3,0 | 2,5 | 2,5 | ||
50 | 4,0 | 3,5 | 3,0 | 2,5 | 2,0 | ||
60 | 5,0 | 3,5 | 3,0 | 2,5 | 2,0 | 2,0 | |
70 | 4,0 | 3,0 | 2,5 | 2,0 | 2,0 | 1,5 | |
80 | 5,0 | 3,5 | 2,5 | 2,0 | 1,5 | 1,5 | 1,5 |
90 | 4,0 | 3,0 | 2,0 | 1,5 | 1,5 | 1,5 | 1,0 |
100 | 3,5 | 2,5 | 1,5 | 1,5 | 1,0 | 1,0 | 0,5 |
Примечание. Поправки более 5 единиц твердости по шкалам В, F, G не допускаются.
Поправки, добавляемые к величинам твердости по Роквеллу при измерениях по шкале С на сферических поверхностях Таблица 5
Твердость по Роквеллу | Диаметр сферы , мм | ||||||||
4 | 6,5 | 8 | 9,5 | 11 | 12,5 | 15 | 20 | 25 | |
55 HRC | 6,4 | 3,9 | 3,2 | 2,7 | 2,3 | 2,0 | 1,7 | 1,3 | 1,0 |
60 HRC | 5,8 | 3,6 | 2,9 | 2,4 | 2,1 | 1,8 | 1,5 | 1,2 | 0,9 |
65 HRC | 5,2 | 3,2 | 2,6 | 2,2 | 1,9 | 1,7 | 1,4 | 1,0 | 0,9 |
(Поправка. ИУС N 8-2002). Значения поправок вычислены по формуле , где HR — значение твердости по Роквеллу, определенное на приборе;
d — диаметр сферы, мм. ИНФОРМАЦИОННЫЕ ДАННЫЕ 1. РАЗРАБОТАН И ВНЕСЕН Центральным научно-исследовательским институтом черных металлов Министерства черной металлургии СССР
2. УТВЕРЖДЕН И ВВЕДЕН В ДЕЙСТВИЕ Комитетом стандартов, мер и измерительных приборов при Совете Министров СССР 04.02.59
3. ВВЕДЕН ВПЕРВЫЕ
4. Стандарт соответствует СТ СЭВ 469-77 и ИСО 6508-86
5. Стандарт унифицирован со стандартом TGL 9011
6. ССЫЛОЧНЫЕ НОРМАТИВНО-ТЕХНИЧЕСКИЕ ДОКУМЕНТЫ
Обозначение НТД, на который дана ссылка | Номер пункта, приложения |
ГОСТ 8.064-94 | Приложение 1 |
ГОСТ 2789-73 | 1.2; 3.3 |
ГОСТ 3722-81 | 3.3 |
ГОСТ 9377-81 | 3.2 |
ГОСТ 23677-79 | 3.1 |
7. Ограничение срока действия снято по протоколу N 4-93 Межгосударственного Совета по стандартизации, метрологии и сертификации (ИУС 4-94) 8. ИЗДАНИЕ (октябрь 2001 г.) с Изменениями N 1, 2, 3, утвержденными в мае 1979 г., октябре 1984 г., мае 1989 г. (ИУС 7-79, 1-85, 8-89)
ВНЕСЕНА поправка, опубликованная в ИУС N 8, 2002 год
Поправка внесена изготовителем базы данных
О компании
МЕТОЛАБ производит современные высокоточные твердомеры для измерения по методам Роквелла, Бринелля, Виккерса.
Источник: metolab.ru
Что такое твердость и как ее измерить?
Твердостью называют свойство материала сопротивляться внедрению в его поверхность индентора.
В чем измеряется твердость?
Существуют два основных способа отображения твердости материалов:
- в килограмм-силы на квадратный миллиметр (кгс/мм 2 );
- может обозначаться буквами HB (HBW), HRB, HRC, HV, HA, HD, HC, HOO и т.д.
По каким методам можно измерять твердость?
В настоящее время разработано много способов определения твердости металлов, таких как:
- измерение твердости вдавливанием под действием статической нагрузки (по методу Бринелля, Роквелла, Супер-Роквелла, Виккерса, М.С.Дрозда, Герца, Лудвика, монотрон Шора, пресс Бринелля);
- измерение твердости динамическим вдавливанием (по методу Мартеля, Польди, вертикальный копер Николаева, пружинный прибор Шоппера и Баумана, маятниковый копер Вальцеля, склероскоп Шора, маятник Герберта, маятниковый склерометр Кузнецова);
- измерение микротвердости статическим вдавливанием (по методу Липса, Егорова, Хрущева, Скворцова, Алехина, Терновского, Шоршорова, Берковича, Кнупа, Петерса,Эмерсона, микротвердомер Цейсса-Ганеманна и др.);
- измерение твердости царапанием (напильником Барба, по Моосу, прибор Мартенса, Хенкинса, микрохарактеризатор Бирбаума, склерометр О’Нейля, Григорович, Беркович).
Среди всех этих способов наибольшую популярность получил способ внедрения индентора под действием статической нагрузки. Основными методами для измерения твердости являются: Бринелль, Роквелл, Виккерс, Шора.
Требования к измерению твердости
К самому распространенному способу измерения твердости, предъявляются следующие требования:
- измерительный прибор должен быть надежным по конструкции, удобным в обращении, универсальным и применимым ко всем без исключения твердым телам, а сама операция по измерению твердости – простой и быстрой;
- вне зависимости от величины прилагаемого усилия или затрачиваемой энергии, значение твердости для однородного тела при постоянной температуре должно быть материальной константой;
- поверхность образца и способ его крепления должны обеспечивать надежную фиксацию, не допускают смещение образца относительно оси приложения нагрузки;
- твердость должна иметь совершенно определенный и ясный физический смысл, и правильную размерность, характеризующую сопротивление материала пластической деформации.
Как рассчитать твердость материала?
Чем выше твердость, тем более высокая нагрузка нужна для определения его твердости. Чем точнее метод, тем выше требования к подготовке испытательной поверхности материала. Соответственно нам необходимо подобрать метод определения твердости, дающий минимальную погрешность при минимальном повреждении поверхности и минимальных затратах на подготовку поверхности к испытанию.
В чем измеряется твердость стали?
Наиболее распространенный способ определения твердости стали — внедрения индентора под действием статической нагрузки по методам Бринелля, Роквелла, Виккерса (см. таблицу 1). И для каждого метода имеется своя шкала измерения твердости.
Твердосплавный сферический индентор
Твердость вычисляется по диагонали отпечатка как нагрузка, деленная на площадь поверхности отпечатка:
Алмазный индентор конической формы с углом при вершине 120° с усилием 60 кгс
Мерой твердости служит разность глубин проникновения наконечника при приложении основной и предварительной нагрузки, измеренная в условных делениях
— при измерении по шкале А (HRA) и С (HRC):
HR = 100-(H-h)/0,002
Разность представляет разность глубин погружения индентора (в миллиметрах) после снятия основной нагрузки и до её приложения (при предварительном нагружении).
— при измерении по шкале B (HRB):
HR = 130-(H-h)/0,002
Твердосплавный сферический индентор с диаметром 1,588 мм (1/2”) и усилием 100 кгс
Алмазный индентор конической формы с углом при вершине 120° с усилием 150 кгс
Прибор Виккерса и Микро-Виккерса
Алмазный индентор пирамидальной формы c 4 гранями
с усилием 1 кгс
с усилием 0,5 кгс
Твердость вычисляется по диагонали отпечатка как нагрузка, деленная на площадь поверхности отпечатка
Нагрузка Р может меняться от 9,8 (1 кгс) до 980 Н (100 кгс). Твердость по Виккерсу HV = 0.189*P/d 2 , МПа, если Р выражена в Н, и HV = 1,854*P/d 2 , кгс/мм 2 , если Р выражена в кгс.
Твердость Н определяют по той же формуле, что и твердость по Виккерсу:
H = 0.189*P/d 2 , если Р выражена в Н.
Алмазный индентор пирамидальной формы c 3 гранями
с усилием 0,1 кгс
Методы статического определения твердости вдавливанием
По методу Герца (1881) | Сдавливание полусферы и плоскости из испытуемого материала до появления следов пластической деформации или трещины | HГ = 6Р/πd 2 кр, кгс/мм 2 |
Монотрон Шора (1900) | Вдавливание алмазного шарика диаметром 0,75 мм или стальных шариков диаметром 1/16″ и 2,5 мм на стандартную глубину 0,045 мм | Мерой твердости служит нагрузка (кгс), необходимая для вдавливания на стандартную глубину |
По методу Лудвика (1907) | Вдавливание стального конуса с углом заострения 90° в плоскость испытуемого тела | Твердость вычисляется как нагрузка, деленная на площадь проекции |
По методу М. С. Дрозда (1958) | Вдавливание шарика нагрузкой Р, измерение глубины восстановленного отпечатка h и критической нагрузки Рs, отвечающей переходу от упругого к остаточному опечатку | Н = (Р-Рs)/πDhвосст, кгс/мм 2 |
Методы динамического определения твердости
По методу Мартеля (1895) | Удар стальной пирамидой, укрепленной на падающем бойке | По энергии удара и диагонали отпечатка определяется твердость H = Е1/V, кгс/мм 2 |
Вертикальный копер Николаева | Удар бойка весом 3 кгс, падающего с высоты 530 мм, по стальному шарику 10 мм, прижатому к изделию | По диаметру отпечатка и тарировонным кривым определяется НВ, кгс/мм 2 |
Пружинный прибор Шоппера | Удар стальным шариком диаметром 10 мм с помощью сжатой пружины | По глубине отпечатка определяется НВ, кгс/мм 2 |
Пружинный прибор Баумана | Удар бойком со стальным шариком диаметром 5 или 10 мм с помощью сжатой пружины с запасом энергии 0,15 и 0,53 кгс·см | По диаметру динамического отпечатка и тарировочным кривым находится НВ, кгс/мм 2 |
Прибор Польди | Удар молотком по бойку, под которым находится эталон и испытуемое тело с зажатым между ними закаленным стальным шариком диаметром 10 мм | По диаметрам отпечатков на образце и эталоне определяется твердость: HВобр = 2 НВэт*d 2 эт/d 2 обр, кгс/мм 2 |
Маятниковый копер Вальцеля (1934) | Удар стальным шариком диаметром 5 или 10 мм, укрепленным на маятниковом копре | Угол отскока в условных единицах |
Склероскоп Шора | Падение бойка весом 2,3 гс с коническим алмазным наконечником с высоты 254 мм | Число условных единиц высоты отскока бойка |
Маятник Герберта | Качание маятника весом 2 или 3 кгс, опирающегося на поверхность испытуемого тела стальным или рубиновым шариком диаметром 1 мм | Бремя 10 односторонних качаний маятника в секунду или амплитуда одного качания в условных единицах |
Маятниковый склерометр Кузнецова (1931) | Качание маятника весом 1 кгс, опирающегося двумя стальными наконечниками или шариками на испытуемое тело | Время затухания колебаний до заданной амплитуды |
Методы статического определения твердости вдавливанием
(микротвердость)
Твердость определяется как отношение нагрузки (в гс) к площади поверхности отпечатка (по диагонали, в мкм)
HV = 1854,4 P/d 2 , кгс/мм 2
Твердость определяется как отношение нагрузки (в кгс) к площади поверхности невосстановленного «отпечатка», исчисляемой по длинной диагонали d (в мм):
Н = 2092 Р/а 2 = 1570 Р/l 2 , кгс/мм 2 ;
Н = ЗR*sin а *Р/l 3 = 4167960Р/l 3 , кгс/мм 2
Н = 18544 P/d 2 , кгс/мм 2
Методы определения твердости царапанием
Источник: metrotest.ru
Что означает «твёрдость стали» или что такое HRC?
Твердость материалов является интегрирующим показателем их механических свойств. Существует эмпирическое соответствие между значением твердости и рядом механических характеристик (например, предел прочности на сжатие, растяжение или изгиб).
С развитием машиностроения возникла необходимость иметь общие методики измерения твердости. В начале XX века профессором Людвигом была разработана теоретическая часть методики определения твердости алмазным конусом. В 1919 году Хью и Стэнли Роквеллы запатентовали гидромеханическую установку, которая получила имя — твердомер Роквелла.
Актуальность этого устройства вызвана необходимостью применения неразрушающих методов контроля твердости в подшипниковой промышленности. Существующий метод Бринелля (HB) основан на измерении площади отпечатка шарика диаметром 10 мм. Отпечаток формируется с помощью шарика из закаленной стали или карбида вольфрама, который вдавливается в образец с определенным усилием.
Метод Бринелля применяется для определения твердости цветных металлов или низколегированных сталей и неприменим для образцов из закаленной стали. Это связано с тем, что рабочая нагрузка составляет 3000 кгс. Шарик деформируется, поэтому метод Бринелля не может считаться неразрушающим методом контроля.
Метод измерения твердости по Роквеллу
Твердость — характеристика материала, противоположная пластичности, способности материала «вытекать» из-под нагрузки. Методика измерения твердости по Роквеллу предназначена для неразрушающего контроля твердости наименее пластичных материалов — сталей и их сплавов. Универсальность метода заключается в наличии трех шкал твердости, которые проградуированы для измерения под одной из трех нагрузок (60, 100 и 150 кгс) для работы с одной из измерительных головок. В качестве рабочего органа измерительной головки применяют алмазный конус с углом 120° и радиусом при вершине 0,2 мм или закаленный шарик диаметром 1/16“ (1,588 мм).
Метод основан на фиксации прямого измерения глубины проникновения твердого тела измерительной головки (индентора) в материал образца. Глубина отпечатка характеризует способность материала сопротивляться внешнему воздействию без образования валика из вытесненного металла вокруг индентора.
Единица твердость по Роквеллу — безразмерная величина, которая выражается в условных единицах до 100. За единицу твердости приняли перемещение индентора на 0,002.
Как измеряется твердость по шкале Роквелла?
Шкала Роквелла измеряет относительную твердость металла. Она основана на том, насколько глубокой является полученная вмятина при ударе тяжелого предмета. Так как же проводят испытания металла?
Во-первых, металл должен быть термически обработан и абсолютно плоским. Иначе результаты теста будут неточными.
Одним из методов является использование конуса с алмазным наконечником для принудительного удара по металлу. Затем тестеры измеряют, насколько глубоко конус проник в поверхность. Затем, это измерение преобразуется в шкалу, которая показывает различные металлы, которые были испытаны, и как они все связаны друг с другом.
Одним из небольших недостатков при испытании клинка ножа является то, что оно оставляет небольшую точечную вмятину на поверхности, что некоторые могут счесть дефектом. Знак испытания может быть скрыт, если испытание проводится в области, которая находится под рукояткой.
Тест Роквелла фактически состоит из двух тестов. Во время первого испытания создается лишь незначительное усилие, используя алмазный наконечник, похожий на карандаш в сверлильном станке. Это гарантирует, что зона испытания абсолютно плоская и является мишенью для основного испытания на давление. После того, как сделано первое измерение, тест повторяется в той же точке. Давление резко возрастает для этого второго теста, при этом приблизительно 150 кг. давления находятся на этом алмазном наконечнике.
Разница между давлением, использованным для первого и второго испытания, представляет собой число твердости по шкале Роквелла. Два (или более) испытания одного и того же куска металла дадут среднее значение для данного конкретного куска стали.
Как устроена шкала твердости по Роквеллу?
Разработано 11 шкал для определения твердости (A…H, K, N, T), которые предназначены для работы в различных комбинациях «интендор – нагрузка». Например, шкалы В, F и G используют для измерения шарик Ø 1,588 с нагрузкой по шкалам В, F — 60 кгс и по шкале G — 150 кгс. Для шкал Е, Н и К применяется шарик Ø 3,175 мм с разными нагрузками.
Распространены такие шкалы:
- А — с конусом и полным усилием на измерительной головке 60 кгс (10 кгс — предварительная нагрузка плюс 50 кгс — основная).
- В — с шариком Ø 1,588 и полным усилием на измерительной головке 100 кгс.
- С — с конусом и полным усилием на измерительной головке 150 кгс.
Предварительная нагрузка, которая позволяет выбрать зазоры твердомера и разрушить окисную пленку на образце, одинакова для измерений с использованием любых шкал.
В качестве индикатора используют устройство часового типа, которое позволяет регистрировать перемещение индентора на 0,002 мм с учетом перемещения рычагов. Максимальное перемещение измерительной головки при рабочей нагрузке — 0,2 мм. На индикаторе расположены шкала, содержащая 100 делений для каждого способа измерения (например, ТК 2 или NOVOTEST ТС-Р).
Диапазоны измерений для шкал (материалы):
- HRA — 20…88 ед. (коррозионностойкие и жаропрочные стали)
- HRB — 20…100 ед. (сплавы меди, ковкий чугун, низкоуглеродистые стали)
- HRC — 20…70 ед. (высокоуглеродистые стали после термической обработки)
Шкалы А и С объединены, шкала В выделена цветом или вынесена отдельно.
Строение шкалы Роквелла
Для испытания твердости металлов методом Роквелла выведено всего 11 шкал. Их отличие состоит в соотношении наконечника и нагрузки. Наконечник может быть не только алмазным конусом, но и шариком из сплава карбида и вольфрама или закаленной стали в форме сферы. Наконечник, закрепленный в установке, называют идентером.
Шкалы принято обозначать буквами латинского алфавита: A, B, C, D, E, F, G, H, K, N, T.
Проводятся испытания прочности основными шкалами — A, B, C:
- Шкала А: испытания алмазным конусом с нагрузкой 60 кгс. Обозначение – HRA. Такие испытания проводятся для тонких твердых материалов (0,3-0,5 мм);
- Шкала B: испытания стальным шариком с нагрузкой 100 кгс. Обозначение – HRB. Испытания проводятся на отоженной мягкой стали и цветных сплавах;
- Шкала C: испытания конусом с нагрузкой 150 кгс. Обозначение – HRC. Испытания проводятся для металлов средней твердости, закаленной и отпущенной стали или слоев толщиной не более 0,5 мм.
Твердость по методу Роквелла принято обозначать HR с третьей буквой шкалы (например, HRA, HRC).
Твердомер по Роквеллу: что это такое и как работает?
Стационарный твердомер представляет собой цельнолитую жесткую П-образную конструкцию (положенную на бок) и состоящую из 2 блоков:
- Измерительный блок (верх) состоит из индикатора часового типа, который контактирует с рычагом подвеса нагрузки. Для исключения возникновения ударной нагрузки при включении режима вдавливания рычаг подвеса имеет гидравлический демпфер.
- Блок установочного перемещения (низ) состоит из винтовой пары с большим шагом для ручного перемещения стола. Винтовая пара служит для создания предварительной нагрузки и больших перемещений стола. Это позволяет измерять твердость на деталях с габаритами, намного превышающими размеры образца толщиной 20 мм. Твердость поверхности стола не ниже HRC 50.
Твердомеры могут иметь двигатель перемещения, электронную систему измерения с дисплеем и другие усовершенствования, не влияющие на методику измерения.
Измерения проводятся при нормальных условиях (температура — 18…23° С, влажность 70…80%).
Требования к образцу:
- образец (деталь) должен лежать устойчиво, не пружинить, не качаться;
- шероховатость поверхности образца не ниже Ra 2,5 по ГОСТ 2789-73.
На партию деталей изготавливают образец, который проходит термическую обработку вместе с деталями.
- образец устанавливают на стол;
- с помощью ходового винта образец подводят к интендору и нагружают предварительно (индикатор выставляется в 0);
- рычагом (кнопкой) включается режим вдавливания интендора в образец;
- при остановке стрелки индикатора (через 2…8 секунд после нагружения) снимают основную нагрузку, считывают значение твердости.
Современные твердомеры Роквелла, оборудованные цифровыми измерительными системами, имеют устройства автоматического подвода, предварительного нагружения, контроля величины усилия и времени рабочей нагрузки. Все усовершенствования должны обеспечивать соответствие требованиям ГОСТ 23677-79.
Формула для расчёта
Твердость материала влияет на глубину проникновения наконечника. Чем испытуемый объект тверже, тем меньшим будет проникновение.
Чтобы численно определить твердость материала, необходима формула. Ее коэффициенты зависят от шкалы. Для снижения погрешности измерений следует принять относительную разницу глубины проникновения индентора в момент приложения основной и предварительной (10 кгс) нагрузки.
Метод измерения твердости по Роквеллу предполагает применение формулы: HR=N-(H-h)/s, где разностью H-h обозначают относительную глубину проникновения индентора под нагрузками (предварительной и основной), величина исчисляется в мм. N, s – это константы, они зависят от конкретной шкалы.
Плюсы и минусы метода
Главным достоинством метода измерения твердости по Роквеллу является его универсальность. Измерения проводят с тремя изменяемыми параметрами, что позволяет расширить сферу его применения.
Другие достоинства метода:
- относится к неразрушающим способам (можно использовать для контроля готовых изделий);
- позволяет контролировать цилиндрические изделия в призме диаметром от 6 мм или с кривизной поверхности R3 с учетом поправок (Прил. 3 по ГОСТ 9013-59 «ИСО 6508-86»);
- позволяет контролировать листовой материал толщиной 0,3…1,0 мм по шкале HRA (супер-роквелл);
- короткое время измерения (не более 2 минут с тестированием на контрольном образце);
- удобство считывания результатов.
К недостаткам относят менее высокую точность и повторяемость измерений по сравнению с методами Бринелля и Виккерса. Однако недостатки сполна компенсируются преимуществами.
Описание
Меры применяются при поверке приборов для измерения твёрдости металлов по методу Роквелла (ГОСТ 9013-59) и Супер-Роквелла (ГОСТ 22975-78).
Меры изготавливаются в виде плиток прямоугольной или круглой формы с одной рабочей поверхностью из углеродистой или легированной стали, алюминия, меди, латуни.
Меры изготавливаются в модификациях МТР-МЕТ, МТСР-МЕТ. Меры МТР-МЕТ предназначены для воспроизведения твёрдости металлов по шкалам Роквелла. Меры МТСР-МЕТ предназначены для воспроизведения твёрдости металлов по шкалам Супер-Роквелла.
Внешний вид мер приведён на рисунке 1.
Твердомер по Роквеллу
Твердомером называется устройство для определения твердости металлов и сплавов методом Роквелла. Он представляет собой прибор с алмазным конусом (или шариком) и материалом, в который конус должен войти. Также приклепляется груз для регулировки силы воздействия.
Время отображает индикатор. Процесс происходит в два этапа: сначала делается нажатие с силой 10 кгс, потом – сильнее. Для большего нажатия применяется конус, для меньшего – шарик.
Исследуемый материал располагается горизонтально. Алмаз опускают на него с помощью рычага. Для плавного спуска в устройстве применена рукоять с масляным амортизатором.
Время основной нагрузки обычно составляет от 3 до 6 секунд, в зависимости от материала. Предварительную нагрузку необходимо сохранять до получения результатов испытания.
Большая стрелка индикатора движется по часовой и отражает результат опыта.
Наиболее популярны в практике такие модели твердомера по методу Роквелла:
- Стационарные приборы «Метротест» модели «ИТР», например, «ИТР-60/150-М».
- Твердомеры Qness GmbH модели Q150R.
- Стационарное автоматизированное устройство TIME Group Inc модель TH300.
Как определить твердость металла по методике Бринелля: особенности
В качестве индентора, то есть самого элемента, который вдавливается в заготовку, используется идеальный шарик диаметром от 1 до 10 миллиметров. Он изготавливается из легированных соединений или из сплава карбида и вольфрама. Регламентируется производство таких шаров ГОСТом 3722 81.
Время, в которое происходит статическое, то есть неподвижное вдавливание, – от 10 до 180 секунд. Этот параметр зависит от материала. Самые минимальные временные промежутки – для чугуна и стали, а более продолжительные – для цветных металлов.
Максимальная нагрузка, которая может быть измерена таким способом, – 450 или 650 НВ, в зависимости от того, из чего сделан шарик.
На образец для правильной деформации подбирается воздействие, посмотрим по формулам в таблице, как можно их вычислить, учитывая, что D – это диаметр шара:
Проверяемый объект | Математически вычисленное изменение |
Свинец или олово | 1d^2 |
Стальные соединения, титан, никель | 30d^2 |
Легкие сплавы | от 2,5d^2 до 15d^2 |
Чугун | 10d^2 или 30d^2 |
Медь и составы с ее добавлением | 5d^2, 10d^2, 30d^2 |
Алгоритм применения метода Бринелля
- Проверяется сам аппарат и тело для внедрения – шар.
- Определяется максимальное усилие.
- Твердомер запускается.
- Измеряется глубина вдавливания.
- Производятся математические вычисления.
Применяемая формула НВ=P/F, где:
- P – нагрузка;
- F – площадь отпечатка.
Следует отметить, что это самый распространенный способ.
Метод Шора
Этот метод является продолжением всем хорошо известного метода «постукивания», когда постукивая по детали или заготовке, мастер пытается определить ее твердость. Метод предложен американский инженером Альбертом Шором в начале XX века. Суть метода заключается в том, что твердость металла определяется по высоте отскока индентора.
Прибор для измерения твердости состоит из полой трубки, на которой по всей длине сделан пропил с нанесенными делениями. Трубка устанавливается на поверхность измеряемого образца и в нее сбрасывается боек с алмазным наконечником. Твердость металла определяется визуально по высоте отскока бойка. По сути, этот прибор является «склерометром».
Данный тип измерений не дает высокой точности, но отлично подходит для экспресс-оценки твердости сплавов на металлургических производствах, когда нужно оперативно определить твердость большой детали или детали, которая имеет сложную поверхность.
Формат отображения твердости по Шору HSD(или HSC, в зависимости от используемой шкалы).
Метод Виккерса
При измерении твердости по методу Виккерса в качестве индентора используется наконечник в форме пирамиды, грани которой сходятся между собой под углом в 136 градусов. Для обеспечения точности испытания важно соблюсти несколько моментов:
- нагрузка должна приходиться строго в центр алмазного наконечника;
- вектор приложения нагрузки должен быть строго перпендикулярен поверхности испытуемого образца.
Измерения происходят по следующему алгоритму: проверяемый образец помещают на специальный стол, сверху в образец происходит вдавливание индентора сразу с необходимым уровнем нагрузки (максимальное возможное значение до 100 кгс). Далее происходит удержание индентора под нагрузкой в течение 10-15 секунд. После снятия индентора происходит измерение глубины вдавливания и диагонали отпечатка.
Далее происходит расчет по форму, где учитывается соотношение приложенной нагрузки к диагонали отпечатка и времени в течение которого происходило испытание. Твердость указывается в формате кгс/мм2, формат отображения HV. Метод Виккерса за счет использования алмазного наконечника позволяет делать более точные измерения, чем метод Бринелля.
Источник: xn--80adbkbsld3ahcppp7ec.xn--p1ai
Что означает твердость hrc 70
Твердостью металла называют его свойство оказывать сопротивление пластической деформации при контактном воздействии стандартного тела-наконечника на поверхностные слои материала.
Испытание на твердость — основной метод оценки качества термообработки изделия.
Определение твердости по методу Бринелля. Метод основан на том, что в плоскую поверхность под нагрузкой внедряют стальной шарик. Число твердости НВ определяется отношением нагрузки к сферической поверхности отпечатка.
Метод Роквелла (HR) основан на статическом вдавливании в испытываемую поверхность наконечника под определенной нагрузкой. В качестве наконечников для материалов с твердостью до 450 HR используют стальной шарик. В этом случае твердость обозначают как HRB. При использовании алмазного конуса твердость обозначают как HRA или HRC (в зависимости от нагрузки).
Твердость по методу Виккерса (HV) определяют путем статического вдавливания в испытуемую поверхность алмазной четырехгранной пирамиды. При испытании измеряют отпечаток с точностью до 0,001 мм при помощи микроскопа, который является составной частью прибора Виккерса.
Метод Шора. Сущность данного метода состоит в определении твердости материала образца по высоте отскакивания бойка, падающего на поверхность испытуемого тела с определенной высоты. Твердость оценивается в условных единицах, пропорциональных высоте отскакивания бойка.
Числа твердости HRC для некоторых деталей и инструментов
Головки откидных болтов, гайки шестигранные, рукоятки зажимные | 33. 38 |
Головки шарнирных винтов, концы и головки установочных винтов, оси шарниров, планки прижимные и съемные, головки винтов с внутренними шестигранными отверстиями, палец поводкового патрона | 35. 40 |
Шлицы круглых гаек | 36. 42 |
Зубчатые колеса, шпонки, прихваты, сухари к станочным пазам | 40. 45 |
Пружинные и стопорные кольца, клинья натяжные | 45. 50 |
Винты самонарезающие, центры токарные, эксцентрики, опоры грибковые и опорные платики, пальцы установочные, цанги | 50. 60 |
Гайки установочные, контргайки, сухари к станочным пазам, эксцентрики круговые, кулачки эксцентриковые, фиксаторы делительных устройств, губки сменные к тискам и патронам, зубчатые колеса | 56. 60 |
Рабочие поверхности калибров — пробок и скоб | 56. 64 |
Копиры, ролики копирные | 58. 63 |
Втулки кондукторные, втулки вращающиеся для расточных борштанг | 60. 64 |
Таблица соотношений между числами твердости по Бринеллю, Роквеллу, Виккерсу, Шору
Указанные значения твердости по Роквеллу, Виккерсу и Шору соответствуют значениям твердости по Бринеллю, определенным с помощью шарика диаметром 10 мм.
65 | 84,5 | — | 2,34 | 688 | 940 | 96 |
64 | 83,5 | — | 2,37 | 670 | 912 | 94 |
63 | 83 | — | 2,39 | 659 | 867 | 93 |
62 | 82,5 | — | 2,42 | 643 | 846 | 92 |
61 | 82 | — | 2,45 | 627 | 818 | 91 |
60 | 81,5 | — | 2,47 | 616 | — | — |
59 | 81 | — | 2,5 | 601 | 756 | 86 |
58 | 80,5 | — | 2,54 | 582 | 704 | 83 |
57 | 80 | — | 2,56 | 573 | 693 | — |
56 | 79 | — | 2,6 | 555 | 653 | 79,5 |
55 | 79 | — | 2,61 | 551 | 644 | — |
54 | 78,5 | — | 2,65 | 534 | 618 | 76,5 |
53 | 78 | — | 2,68 | 522 | 594 | — |
52 | 77,5 | — | 2,71 | 510 | 578 | — |
51 | 76 | — | 2,75 | 495 | 56 | 71 |
50 | 76 | — | 2,76 | 492 | 549 | — |
49 | 76 | — | 2,81 | 474 | 528 | — |
48 | 75 | — | 2,85 | 461 | 509 | 65,5 |
47 | 74 | — | 2,9 | 444 | 484 | 63,5 |
46 | 73,5 | — | 2,93 | 435 | 469 | — |
45 | 73 | — | 2,95 | 429 | 461 | 61,5 |
44 | 73 | — | 3 | 415 | 442 | 59,5 |
42 | 72 | — | 3,06 | 398 | 419 | — |
40 | 71 | — | 3,14 | 378 | 395 | 54 |
38 | 69 | — | 3,24 | 354 | 366 | 50 |
36 | 68 | — | 3,34 | 333 | 342 | — |
34 | 67 | — | 3,44 | 313 | 319 | 44 |
32 | 67 | — | 3,52 | 298 | 302 | — |
30 | 66 | — | 3,6 | 285 | 288 | 40,5 |
28 | 65 | — | 3,7 | 269 | 271 | 38,5 |
26 | 64 | — | 3,8 | 255 | 256 | 36,5 |
24 | 63 | 100 | 3,9 | 241 | 242 | 34,5 |
22 | 62 | 98 | 4 | 229 | 229 | 32,5 |
20 | 61 | 97 | 4,1 | 217 | 217 | 31 |
18 | 60 | 95 | 4,2 | 207 | 206 | 29,5 |
— | 59 | 93 | 4,26 | 200 | 199 | — |
— | 58 | — | 4,34 | 193 | 192 | 27,5 |
— | 57 | 91 | 4,4 | 187 | 186 | 27 |
— | 56 | 89 | 4,48 | 180 | 179 | 25 |
Отверстия под резьбу
Таблица сверл для отверстий под нарезание трубной цилиндрической резьбы.
Размеры гаек под ключ
Основные размеры под ключ для шестигранных головок болтов и шестигранных гаек.
G и M коды
Примеры, описание и расшифровка Ж и М кодов для создания управляющих программ на фрезерных и токарных станках с ЧПУ.
Типы резьб
Типы и характеристики метрической, трубной, упорной, трапецеидальной и круглой резьбы.
Масштабы чертежей
Стандартные масштабы изображений деталей на машиностроительных и строительных чертежах.
Режимы резания
Онлайн калькулятор для расчета режимов резания при точении.
Отверстия под резьбу
Таблица сверл и отверстий для нарезания метрической резьбы c крупным (основным) шагом.
Станки с ЧПУ
Классификация станков с ЧПУ, станки с ЧПУ по металлу для точения, фрезерования, сверления, расточки, нарезания резьбы, развёртывания, зенкерования.
Режимы резания
Онлайн калькулятор для расчета режимов резания при фрезеровании.
Форматы чертежей
Таблица размеров сторон основных и дополнительных форматов листов чертежей.
CAD/CAM/CAE системы
Системы автоматизированного проектирования САПР, 3D программы для проектирования, моделирования и создания 3d моделей.
Чтение чертежей
Техническое черчение, правила выполнения чертежей деталей и сборочных чертежей.
Ме́тод Рокве́лла — метод неразрушающей проверки твёрдости материалов. Основан на измерении глубины проникновения твёрдого наконечника индентора в исследуемый материал при приложении одинаковой для каждой шкалы твердости нагрузкой, в зависимости от шкалы обычно 60, 100 и 150 кгс.
В качестве инденторов в методе применяются прочные шарики и алмазные конусы с углом при вершине 120° со скруглённым острым концом.
Из-за своей простоты, скорости по сравнению с другими методами и воспроизводимости результатов он является одним из наиболее распространённых методов испытаний материалов на твёрдость.
История [ править | править код ]
Измерение твёрдости по относительной глубине проникновения индентора было предложено в 1908 году венским профессором Людвигом (Ludwig) в книге «Die Kegelprobe» (дословно «испытание конусом») [1] .
Метод определения относительной глубины проникновения индентора, предложенный Хью и Стэнли Роквеллами, исключал ошибки, связанные с механическими несовершенствами измерительной системы, такими, как люфты и поверхностные дефекты и загрязнения испытуемых материалов и деталей.
Твердомер Роквелла, прибор для определения относительной глубины проникновения, был изобретён уроженцами штата Коннектикут Хью М. Роквеллом (1890—1957) и Стэнли П. Роквеллом (1886—1940). Потребность в этом устройстве была вызвана необходимостью оперативного определения результатов термообработки обойм стальных шарикоподшипников. Метод Бринелля, изобретённый в 1900 году в Швеции, был медленным, не применимым для закалённых сталей, и оставлял слишком большой отпечаток, чтобы считать этот метод методом неразрушающего контроля.
Патентную заявку на новое устройство они подали 15 июля 1914 года; после её рассмотрения был выдан патент № 1294171 от 11 февраля 1919 года [2] .
Во время изобретения Хью и Стэнли Роквеллы (они не были прямыми родственниками) работали в компании New Departure Manufacturing (Бристоль, Коннектикут). New Departure, бывшая крупным производителем шарикоподшипников, в 1916 году стала частью United Motors, а затем — корпорации General Motors.
После ухода из компании в Коннектикуте, Стэнли Роквелл переехал в Сиракьюс (штат Нью-Йорк) и 11 сентября 1919 года подал заявку на усовершенствование первоначального изобретения, которая была утверждена 18 ноября 1924 года. Новый прибор был также запатентован под № 1516207 [3] [4] . В 1921 году Роквелл переехал в Западный Хартфорд, в Коннектикуте, где сделал дополнительные усовершенствования [4] .
В 1920 году Стэнли Роквелл начал сотрудничество с производителем инструментов Чарльзом Вильсоном (Charles H. Wilson) из компании Wilson-Mauelen с целью коммерциализации изобретения и разработки стандартизированных испытательных машин [5] .
Около 1923 года Стэнли Роквелл основал фирму по термообработке Stanley P. Rockwell Company, которая существует до сих пор в Хартфорде, в Коннектикуте. Через несколько лет она, переименованная в Wilson Mechanical Instrument Company, сменила владельца. В 1993 году компанию приобрела корпорация Instron.
Шкалы твёрдости по Роквеллу [ править | править код ]
Стандартами нормировано 11 шкал определения твердости по методу Роквелла (A; B; C; D; E; F; G; H; K; N; T), эти шкалы различаются типом индентора, испытательной нагрузкой и константами в формуле для вычисления твёрдости по результатам измерения [6] .
Наиболее широко используются два-три индентора: сферический в виде шарика из карбида вольфрама или инструментальной закалённой стали диаметром 1/16 дюйма (1,5875 мм) или шарик диаметром 1/8 дюйма и конический алмазный наконечник с углом при скруглённой вершине 120°. Стандарты предусматривает в зависимости от шкалы 3 фиксированные нагрузки при вдавливании индентора — 60, 100 и 150 кгс.
Численная величина твёрдости определяется по формуле, коэффициенты в которой зависят от шкалы. Для снижения ошибки измерения от состояния испытуемой поверхности принимается относительная разница в глубине проникновения индентора при приложении основной и предварительной (10 кгс) нагрузки (см. рисунок).
Для обозначения твёрдости, определённой по методу Роквелла, используется сокращение HR, с 3-й буквой, указывающая на шкалу, по которой проводились испытания (HRA, HRB, HRC и т. д. до HRT). Например, HRC 64.
Наиболее широко используемые шкалы твёрдости по Роквеллу
Формулы для определения твёрдости [ править | править код ]
Чем твёрже материал, тем меньше будет глубина проникновения наконечника в него. Чтобы при большей твёрдости материала не получалось меньшее число твёрдости по Роквеллу, твёрдость определяют по формуле:
H R = N − H − h s >> где разность H − h — относительная глубина проникновения индентора под предварительной и основной нагрузками в мм, N , s — константы, зависящие от конкретной шкалы Роквелла (см. таблицу).
Таким образом, твердость по Роквеллу является безразмерной величиной.
Наиболее часто используемые шкалы Роквелла [7]
Методика проведения испытания промышленным твердомером Роквелла [ править | править код ]
- Выбрать подходящую для проверяемого материала шкалу (А, В или С).
- Установить соответствующий индентор и нагрузку.
- Перед тем, окончательным измерение надо сделать два пробных, неучитываемых отпечатка, чтобы проверить правильность установки индентора и стола.
- Установить эталонный блок на столик прибора.
- Приложить предварительную нагрузку в 10 кгс, обнулить шкалу.
- Приложить основную нагрузку и дождаться достижения максимального усилия.
- Снять нагрузку.
- Прочесть на циферблате по соответствующей шкале значение твёрдости (цифровой прибор показывает на экране значение твёрдости).
- Порядок действий при проверке твёрдости испытуемого образца такой же, как и на эталонном блоке. Допускается делать по одному измерению на образце при проверке массовой продукции.
Факторы, влияющие на точность измерения [ править | править код ]
- Важным фактором является толщина образца. Не допускается проверка образцов с толщиной менее десятикратной глубины проникновения наконечника.
- Ограничивается минимальное расстояние между отпечатками (3 диаметра между центрами ближайших отпечатков).
- Параллакс при считывании результатов с циферблата стрелочных приборов.
Сравнение шкал твёрдости [ править | править код ]
Простота метода Роквелла (главным образом, отсутствие необходимости измерять диаметр отпечатка) привела к его широкому применению в промышленности для проверки твёрдости. Также не требуется высокая чистота измеряемой поверхности (например, методы Бринелля и Виккерса включают замер отпечатка с помощью микроскопа и требуют полировки поверхности).
К недостатку метода Роквелла относится меньшая точность по сравнению с методами Бринелля и Виккерса.
Существует корреляция между значениями твёрдости, измеренной разными методами (например, см. рисунок — перевод единиц твёрдости HRB в твёрдость по методу Бринелля для алюминиевых сплавов). Зависимость носит нелинейный характер. Существуют нормативные документы, где приведено сравнение значений твёрдости, измеренной разными методами (например, ASTM E-140).
Оценка механических свойств по испытаниям на твёрдость [ править | править код ]
Связь между результатами проверки на твёрдость по Роквеллу и прочностными характеристиками материалов исследовались такими учёными-материаловедами, как Н. Н. Давиденков, М. П. Марковец и др.
Используются методы определения предела текучести по результатам проверки на твёрдость вдавливанием. Такая связь была найдена, например, для высокохромистых нержавеющих сталей после различных режимов термообработки. Среднее отклонение результатов методов для конического алмазного индентора составляло всего +0,9 %.
Были также проведены исследования по нахождению связи между значениями твёрдости и другими прочностными характеристиками, определяемыми при растяжении, такими, как предел прочности (временное сопротивление), относительное сужение и истинное сопротивление разрушению.
Твердость клинков современных кухонных ножей принято определять в единицах по шкале Роквелла. Показатель в 40-45 единиц считается низким и соответствует изделиям из мягких металлов, а значение 60-63 соответствует лезвиям высокой твердости. Например, ножи SuncraftMU соответствуют значению 59 HRC, и это очень высокий показатель.
Однако, для обычного пользователя сложная производственная терминология мало понятна. Что, например, представляет собой упомянутая выше шкала Роквелла, и какое значение твердости можно считать оптимальным для кухонного ножа?
Методом Роквелла принятой называть самый простой и доступный способ определения твердости металлов, основанный на проникновении твердого наконечника твердомера вглубь материала и измерении глубины такого проникновения. Метод назван именем американских изобретателей Роквеллов, которые в начале 20-х годов прошлого века сконструировали и запатентовали твердомер – машину для определения глубины проникновения наконечника в металл.
Сегодня известно 11 шкал определения твердости — A; B; C; D; E; F; G; H; K; N; T. Все они имеют свои особенности и специфику измерения, а полученный результат обозначается символом HR, к которому добавляется буква, соответствующая шкале измерения. Поскольку твердость ножей измеряется единицами HRC, нас интересует шкала С.
В соответствии с условиями проведения тестирования по шкале С, величина твердости измеряется как разница глубины проникновения алмазного конуса с углом 120° в области вершины при приложении нагрузки 150 кгс. Чем тверже материал, тем меньше будет проникновение наконечника.
Максимальный показатель твердости для ножевой стали составляет 70 HRC, но на практике инструменты, значение HRC по Роквеллу которых превышает 65 единиц, не встречаются. Этому есть простое объяснение: чем тверже металл, тем более он хрупкий, что для ножа очень даже плохо. Поэтому оптимальным решением для кухонных ножей является использование стали с твердостью 56-62 HRC, а если это значение выше, то лезвие обязательно защищается обкладками из более мягкого материала, как, например, в изделиях из дамасской стали.
Самостоятельно измерить показатель HRC по Роквеллу в домашних условиях без наличия твердомера практически невозможно, поэтому при покупке ножей стоит выбирать продукцию проверенных производителей, таких, как японский бренд Suncraft.
Источник: master-kleit.ru